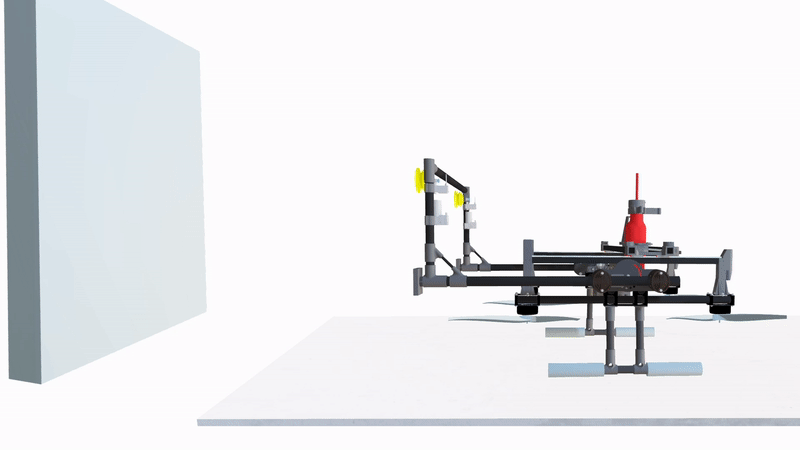
Flying and Perching
After flying to the desired site on the asset, our custom attachment system perches the drone on all surfaces. Power for continuous operation is provided by a power tether.
Our solution allows you to get better data on your asset at the right time. Instead of going on instinct and experiences from other assets, we can provide you with high-quality insights. This makes planning easier, keeps initial inspection costs low and prevents expensive errors down the line.
Every asset is different – get in touch to discuss how AITHON Robotics can help you!
For man-made surfaces, the attachment is robust and reliable. We have tested and deployed on concrete with various degrees of deterioration, including cracks, dirt, and wet surfaces.
Get in touch to learn if AITHON Robotics works for you!
For non-destructive testing:
For destructive testing:
Do you have other inspection tools? Let us know to discuss how we can get the best data in the best way!
Our solution allows for rapid sensor placement and movement. Without having to set up scaffolding, you can get insights into accelerations, strains and displacements.
We’re happy to accomodate your specific needs – get in touch now!
We don’t stop until the work is done – by operating as a tethered drone, mission durations are not limited.
No – our team operates the drone according to your needs and requirements so that you can focus on what you do best: keeping assets safe!
After flying to the desired site on the asset, our custom attachment system perches the drone on all surfaces. Power for continuous operation is provided by a power tether.
Once perched, the drone can rotate such that the thrust is perpendicular to the wall. This design keeps payloads at the optimal location for flight performance, as well as making the most of the possible space on the drone.
Interaction is only useful, if it is precise. A positioning system allows for tools to be positioned and sensors to be deployed at exactly the right position. For scanning tasks, instruments can be repeatedly moved to ensure best data quality.
Taking core samples, drilling holes or screwing sensors requires large forces. The propellers support the mechanism in providing these. During the interaction, the pilot can monitor progress and intervene if needed.